Closing the Loop
Steelcase supports Gabriel’s ambitious recycling program with up to 17 tons of material scraps per year
The amount of waste flooding our planet plays a major part in the climate crisis. Textile waste contributes significantly to greenhouse gas emissions and environmental degradation. Only a fraction of the 92 million tons of textile waste produced each year worldwide is reused or recycled. The remainder finds its way to landfills or incinerators. As people become more aware of this daunting problem, the demand for sustainable fabrics in all business sectors – including the furniture industry – is growing.
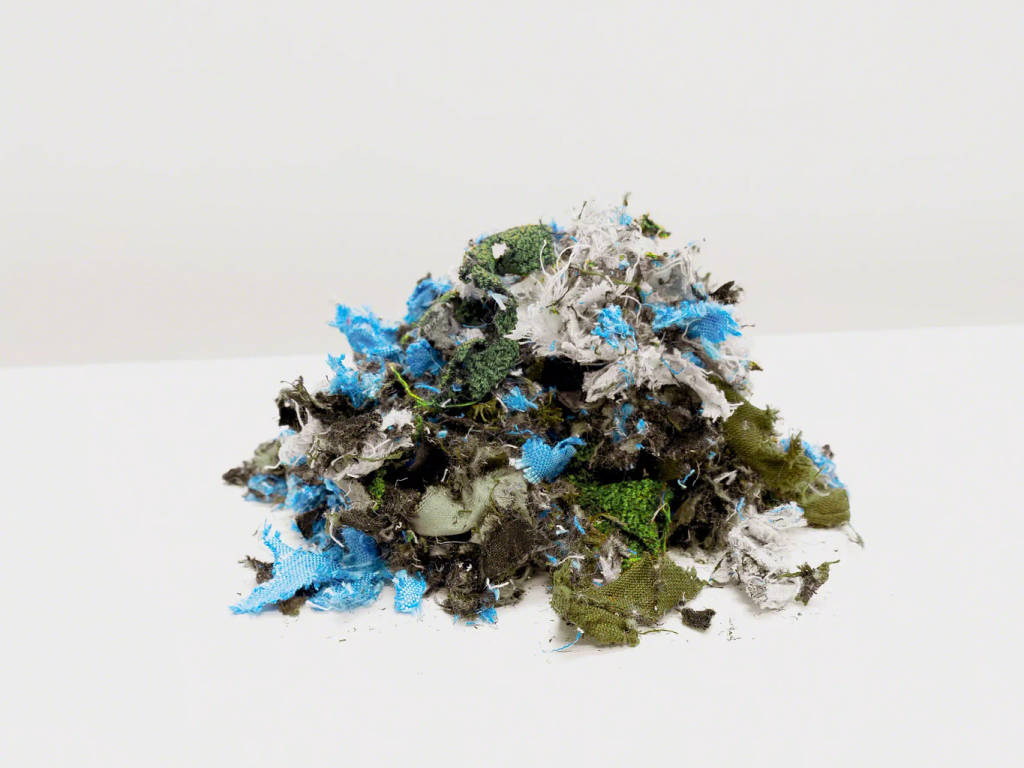
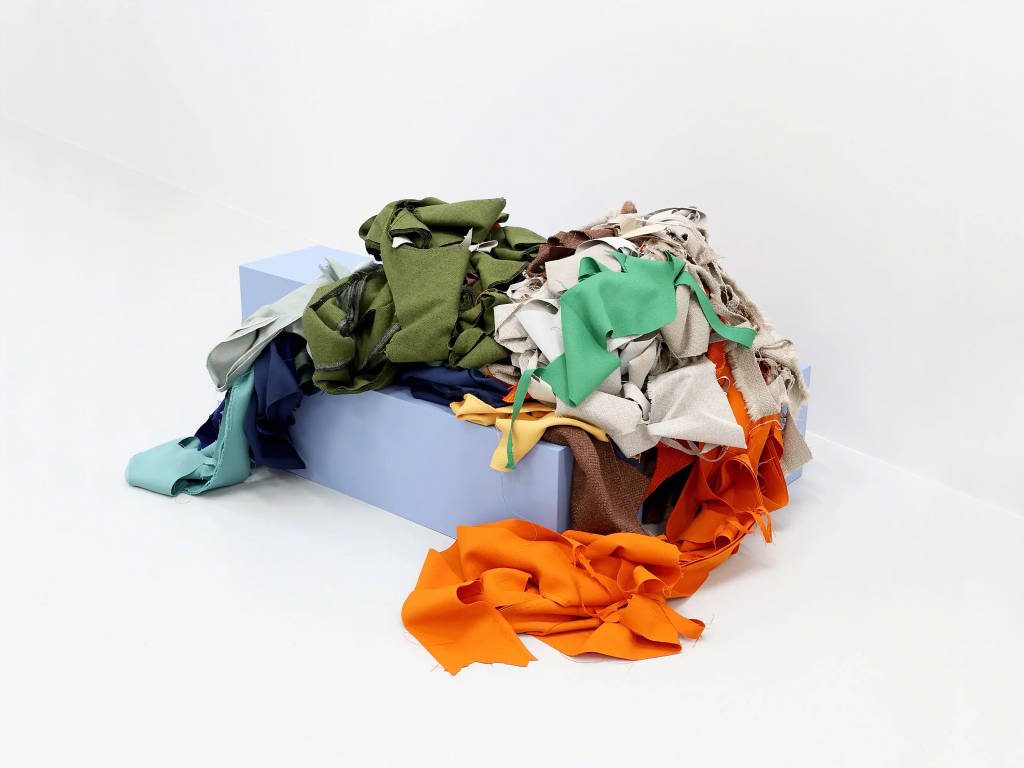
“It is time to leave the throwaway culture behind and embrace waste as a valuable resource.“
Jeppe Emil MogensenDesign Director, Gabriel
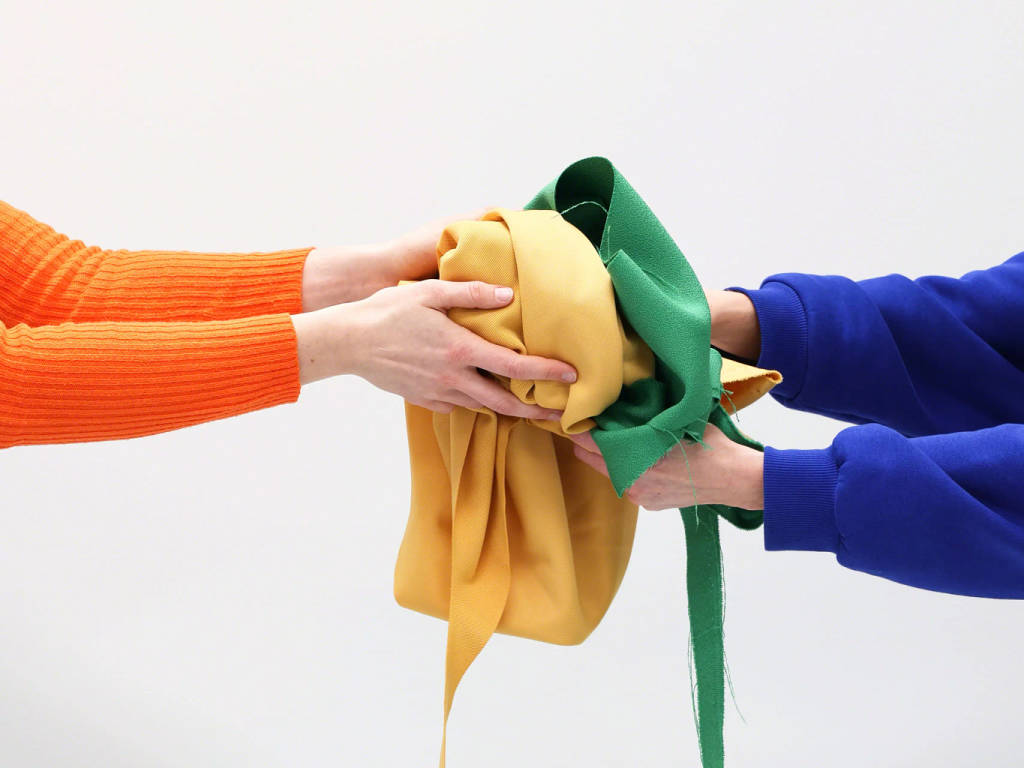
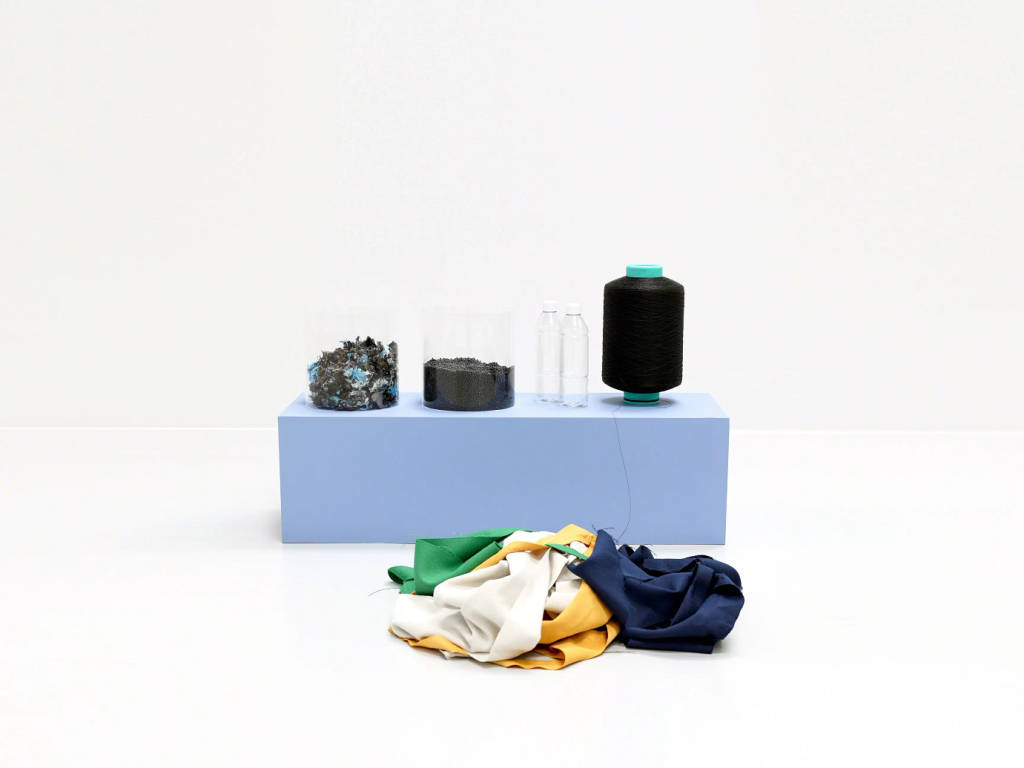
Steelcase has been relentlessly looking for innovative fabric solutions as part of its long-standing commitments to designing for circularity and choosing and using materials responsibly. In the United States, the company started to explore ways to recycle fabric scraps from its own production process as early as 2011. In 2017, with the help of its supplier Duvaltex, Steelcase introduced the New Black collection: a range of sustainable fabrics made of scrap panel fabric and PET from recycled bottles.
Inspired by this successful – and sustainable – partnership, teams at the Steelcase Sarrebourg manufacturing facility in France, which produces chairs for Europe, the Middle-East and Africa, looked for a local partner who shared this same ambition. “We started discussions with our textile supplier Gabriel, who was in the process of designing a revolutionary textile-to-textile recycling program and was in need of a partner to provide them with textile waste,” recalls Andrea Korsten, Steelcase product manager. “It was a perfect match.”
Gabriel’s vision was to design a fabric that would come from used materials – including textile waste – and could be recycled again and again to create new textiles. “It is time to leave the throwaway culture behind and embrace waste as a valuable resource,” explains Jeppe Emil Mogensen, design director at Gabriel.
Gabriel’s goal is three-fold: to create an eco-friendly range of products, to ensure the same quality standards as any other Gabriel fabric and to create a beautiful design that would appeal to a wide variety of customers. “It’s this combination of sustainability, functionality and aesthetics that makes Loop so unique,” adds Mogensen.
To play a meaningful part in Gabriel’s take-back system, the Steelcase plant in Sarrebourg had to define a well-thought-out waste management process, including fabric scraps sorting and collection, as well as exploring ways these could be compacted and transported.
Once delivered to Gabriel’s recycling unit, the textile waste-bales from Steelcase’s manufacturing plant are shredded and melted into pellets, which are then mixed with post-consumer recycled polyester from used plastic bottles. These materials are melted again and spun into a new yarn, which can then follow Gabriel’s usual production process. The result is a new textile made entirely of waste.
“It took about one year for the Sarrebourg team to implement the project as the process requires a lot of preparation and knowhow,” underlines Christophe Bonnet, quality engineer at Steelcase. “We carried out a number of tests to identify which fabrics could be part of that take-back system, and we reconfigured the cutting production line to make room for the containers. We also trained employees to recognize the right scraps among 100 different fabrics and meticulously remove any elements, like plastic or paper, that could pollute the process. This step is critical – if not done very carefully, it could compromise the ability for Gabriel to reuse the material.”
“Gabriel Loop is truly a circular solution that strives to make the best possible design decision that does the least amount of damage possible to our planet,” says Mogensen. Convinced that this closed-loop system is the right way forward, Steelcase is now exploring more ways to design for circularity, including recycling more fabrics and involving additional manufacturing facilities in the take-back system. “Designing out waste, building long-lasting products and supporting responsible end-of-life management is our way of helping to create a more sustainable future,” explains Korsten.
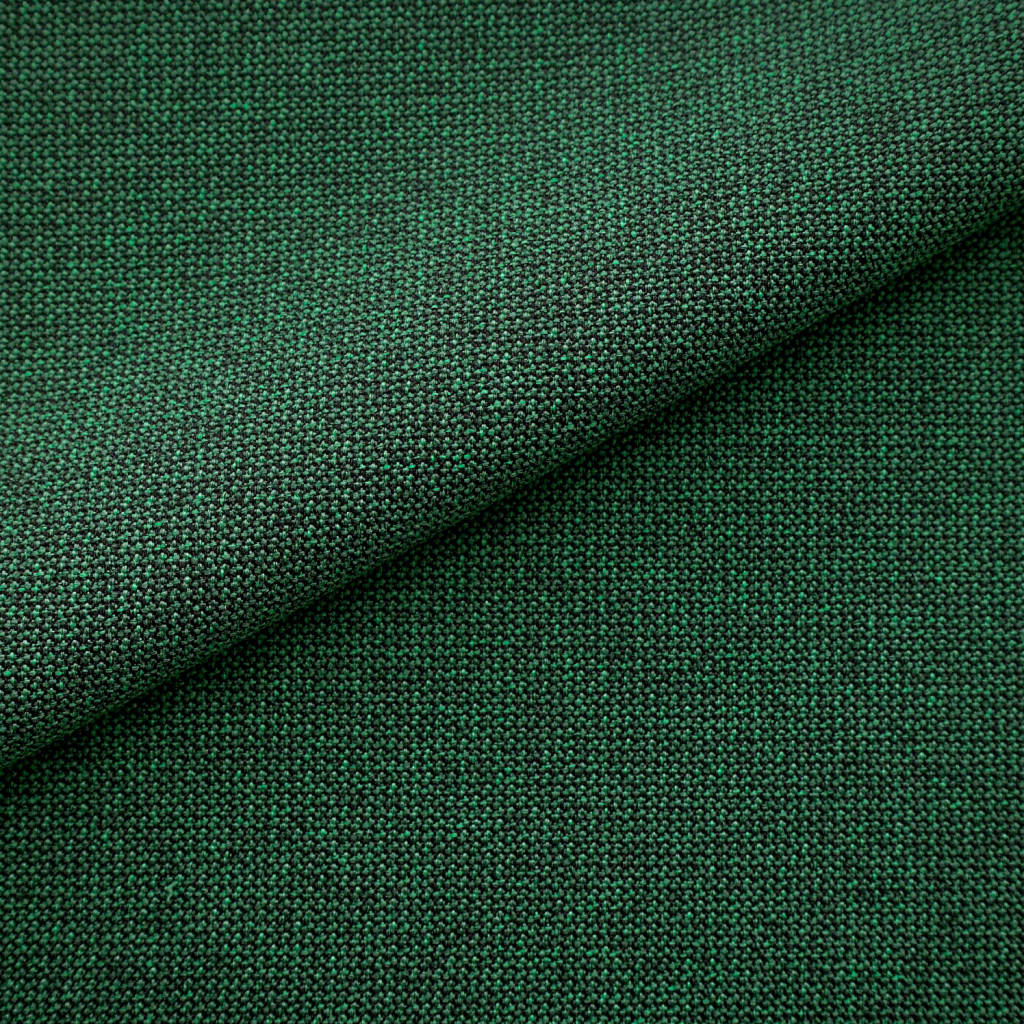
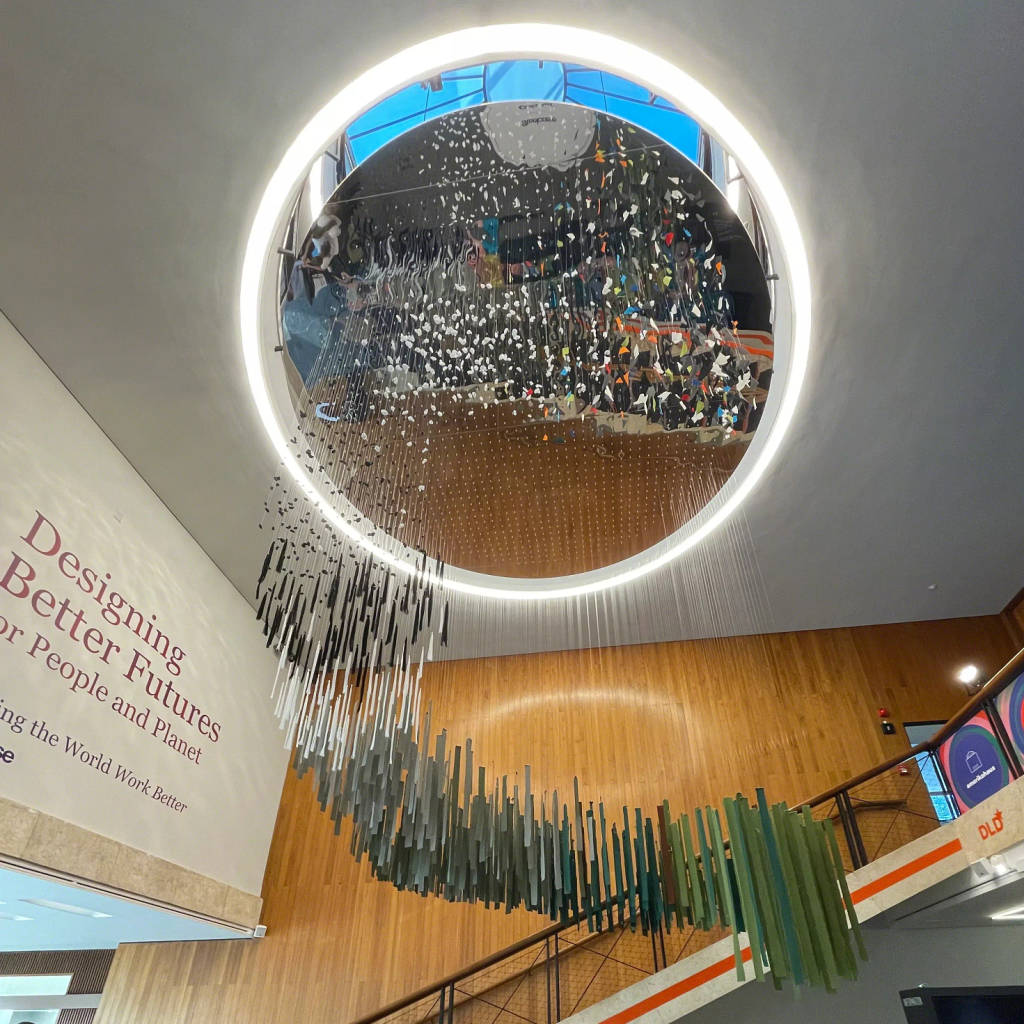
Explore Steelcase’s actions for People and the Planet.