Safeguarding Your Workplace Against Virus Transmission
Key considerations:
- How many people use a space on a daily basis? The more people using a space, the greater the risk of transmission.
- How often is a surface touched? For example, a table base is less likely to transmit germs than a door handle.
- How often will a space be cleaned?
These 3 factors should be considered together.
- Chair controls are high-touch, but if the chair is only used by one person, that’s less concerning.
- But the door handle of a frequently used meeting room is both high touch and high use, so it should be prioritized.
Bottom line: Focus on high-touch, multi-user surfaces.
How to Sanitize Your Steelcase Products
Fabrics + Soft Surfaces
Do not use disinfectants unless the fabric is specifically approved for this. Disinfectants will damage most fabrics.
Ask yourself: Is deep-cleaning necessary?
- SARS-CoV-2, the virus that causes COVID-19, is mainly spread via aerosol, not surfaces.
- Coronaviruses on surfaces and objects is naturally destroyed within hours to days.
- Fabrics rarely transmit contagions. Studies show viruses stay active on porous materials a much shorter time than nonporous surfaces.
- Even for microbes that are spread via surface, soap and water are enough. This removes microbes from surfaces, which lowers the risk of transmission.
- Fabrics are typically on low-touch surfaces, whereas the greatest risk of touch transmission comes from high-touch, multi-user surfaces.
If you do want to deep clean soft surfaces, follow these steps:
- Mix 1 part clear dish detergent and 16 parts water in a spray bottle.
- Spray soft surface lightly and evenly until damp. The spray should coat the surface but not soak through.
- Let sit for 1-2 minutes.
- Use a wet/dry vacuum (such as a Shop Vac) to remove all moisture from the surface.
- Allow to air dry until completely dry.
Hard Surfaces (Glass, Plastic, Laminate, Paint, Wood, Metal, etc.)
All Steelcase standard hard surfaces can be disinfected as follows:
- Use one of the 5 cleaners listed below.
- Spray hard surfaces lightly and evenly.
- Wipe dry.
Approved Disinfectants for Hard Surfaces:
These are the only disinfectants that are EPA-approved as effective against the SARS-CoV-2 virus and that are proven not to negatively impact material finish. Damage caused by using any cleaning products except these will not be covered by warranty.
- Lysol Disinfecting Wipes
- Formula 409 Disinfecting Spray
- Clorox Non-Bleach Disinfecting Wipes
- Lysol All Purpose Spray Cleaner
- Fantastik All Purpose Spray Cleaner
Can’t Find Any of These Disinfectants?
If you can’t find one of these approved disinfectants, you can use instead a 1:16 dishsoap/water mixture in a spray bottle. Let sit for 1-2 minutes, then wipe dry.
Download a print version of hard and soft surface cleaning instructions.
Video Tutorial
To demonstrate proper technique for reducing risk of virus transmission without damaging your product’s finish, watch this video.
Our Stance on Antimicrobials
“ANTIMICROBIAL” ≠ “AnTI-VIRAL”
It’s important to keep in mind that the word “antimicrobial’ is a generic term, and it’s used pretty loosely. The word “antimicrobial” basically means something that destroys or inhibits the growth of microorganisms.
Most antimicrobial products only work against 1 or 2 types of microorganisms, which is why it’s important to read the fine print on any antimicrobial product claim. For example, some may work only against bacteria but not viruses.
We prefer to use the terms antiviral or “virus-inhibiting,” because these terms are specific to the microorganism of interest, SARS-CoV-2.
ARE ANTIMICROBIALS A WAY TO COMBAT COVID-19?
If a company makes these kinds of claims, read the fine print. For example, some products may be antimicrobial but only effective against bacteria. Only a few antimicrobial products have been approved by the EPA to claim efficacy against SARS-CoV-2.
The CDC still says the most effective ways of limiting the spread of coronavirus are to:
- Wash hands thoroughly and often
- Practice social distancing
- Arrange your space to facilitate social distancing
- Wear masks
- Clean surfaces that are touched by multiple people frequently
HOW WE’RE THINKING ABOUT ANTIMICROBIALS
Our Product Development teams are beginning to look at antimicrobial materials like copper. (One study found that no viable SARS-CoV-2 virus was measured after 4 hours on copper, vs. up to 72 hours on plastic and stainless steel).
We now offer a copper door handle as an option for our architectural products – ask your Steelcase salesperson or dealer for details. Solutions like these can help augment cleaning protocols and lower transmission risk.
Remember, though: Antimicrobial materials still need to be cleaned regularly.
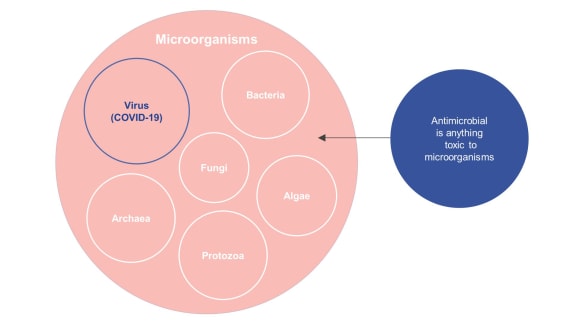
A substance can be antimicrobial or antiviral because of:
- A chemical additive in the engineered formulation, for example in paint coatings or on fabrics;
- An inherent material attribute, for example for the substance copper, where there is an inherent mechanism in that substance that is unfriendly to microorganisms;
- Or a physical structure, like micropatterned Sharklet, which has an engineered structure that acts to repel microorganisms
Frequently Asked Questions
Can I use any cleaning products besides the ones you recommend?
Contract surface materials aren’t designed to withstand harsh chemicals. The image here shows what happened to the paint on a new Steelcase storage tower when a non-approved disinfectant was used on it.
Steelcase’s Materials Lab ran over 160,000 test cycles to find which cleaning products would work against COVID-19 without damaging our products. It’s impossible to test every product and every surface material, so the ones we recommend are our best attempt at finding products that are effective and widely available in North America.
If in doubt, test the cleaning product on an inconspicuous area before using widely. And remember: The CDC says soap and water are effective at mitigating virus spread. After all, that’s what we use on our hands! If you can’t find one of the 5 disinfectants we recommend for our hard surfaces, simply use a 1:16 dishsoap/water mixture in a spray bottle. Spray the hard surface, let sit for a minute, then wipe dry.
Is it OK to use bleach?
No, unless the material is specifically designed to be bleach-cleanable. For a list of these materials, see the Finish Library and filter by “bleach cleanable.”
I don’t have bleach-cleanable materials on my chairs and/or panels. How do I clean them?
See instructions on this page under "How To Sanitize Your Steelcase Products." DO NOT use any cleaning products besides the ones we recommend. The image to the right shows the damage to the paint of a new Steelcase storage tower when someone used a non-approved disinfectant on it.
What about my Steelcase partner products?
Steelcase can only provide guidance on products we manufacture. For questions about products manufactured by our partner brands, refer to those manufacturers’ websites.
How do I clean my Steelcase office chair?
Follow the instructions on this page for how to clean both hard and soft surfaces, depending on which part of the chair you want to clean. Note, though, that …
- COVID-19 is spread mainly via aerosol, not surfaces
- Germs are mainly spread via high-touch surfaces that are touched by multiple users, like chair armcaps. (Not many people touch chair seats, for example.) If you are the only person who sits in your chair, the chance of microbe transmission is almost non-existent.
That said, if you’d like to clean your chair, see our instructions above or watch the video.
Are there special instructions for cleaning electronic products, like task lights, height adjust desk controllers and powerstrips?
To clean electronic type products and components, use a disinfectant wipe or a cloth sprayed with a disinfectant cleaner. Do not use a high-concentration bleach solution. Do not spray cleaning solution directly onto the product or electronic component. Apply a gentle swipe when cleaning - no need to rub or scrub the surface.
What about some of the cleaning technologies such as electrostatic chemical sprayers or UV light? Are those safe and/or effective on Steelcase products?
The problem with these technologies is that interiors have a bunch of different materials and components (wood, metal, laminate, fabric ... not to mention artwork, carpet, etc.). So using something like an electrostatic sprayer means spraying all of these surfaces with the same disinfectant, which could damage some surfaces. Therefore, we don't recommend using this method to clean interiors that include our products.
These are some of the tests that our Materials Lab is currently conducting, and we hope to have more info soon. Until we have more data, we recommend using the products and techniques outlined on this page.
What about my Steelcase Boundary Tent?
For stain removal, see the Surface Materials Reference Manual.
For disinfecting – we do not recommend disinfecting tent products. They are low-risk for potential microbe transmission - first, because few people typically touch them, and secondly, because they are made of porous material. Research has found that virus microbes remain viable on porous materials a much shorter time than on non-porous surfaces like plastic or laminate.
What disinfectants are OK to use on Foundation, Brisa and StandIn?
Foundation, Brisa and Stand In are our three most popular durable materials, and their manufacturers have provided the guidance below on the use of a broad selection of disinfecting cleaners.
Foundation (look under the “Faux Leather Featuring Resilience” column)
Brisa
Stand In
A fresh water rinse after application of harsh commercial cleaners is required.
Rating System
- No Effect: no change in color or surface finish
- Slight Effect: a change in color or surface finish only visible at certain angles or directions
- Moderate Effect: a change in color or surface finish that is visible from all angles and directions
- Severe Effect: a change in color or surface finish, which obviously and markedly alters the original condition of the specimen
- Cracking, Peeling, or Bubbling: Not acceptable
What Steelcase fabrics are bleach cleanable?
Steelcase has many fabrics in its standard and graded in programs that are bleach cleanable. The full list can be found here.
DISCLAIMER
The test method is to evaluate the material's relative resistance or compatibility to specific cleaner and/or disinfectant chemistries and is not an approval or recommendation of said cleaners and/or disinfectants. This test method is not intended to replicate a 'real world' scenario as there is no way to predict use (or misuse) of cleaners and/or disinfectants within an environment.
Important Notes Regarding These Cleaning Instructions
- For the latest information on potential exposure pathways for COVID-19 infection, including contact with surfaces, please see the CDC website.
- Before using any cleaner, check first to ensure it complies with your company’s EHS (Environmental Health and Safety) requirements.
- Please work with your Facilities and EHS staff to determine how frequently your products should be cleaned.
- Always follow the cleaner manufacturer’s instructions for use, including dilution and dwell time (time that the cleaner remains on surface before being cleaned off).
- Proper personal protection equipment (PPE) such as gloves and eye protection, as directed by the cleaner manufacturer, must be worn.
- Never mix cleaners together, especially bleach and ammonia, as the mixture produces toxic fumes.
- Ensure that proper ventilation is used during cleaning, in accordance with the cleaner manufacturer’s directions.
- To avoid risks of fire or shock, always disconnect electrical power when cleaning products that use or provide electricity.
- Be careful not to allow liquids to enter any openings in electrical products.
- Since these types of cleaners are marketed under a large number of brand names, it isn’t possible to evaluate all cleaners on all surfaces.
- Due to the wide variation in the end use of these cleaning products (including amount of product applied, elapsed time before removal from the surface, physical action used to remove the cleaner, and the number of applications), your results may vary from the test results used to develop this guide.
- If you are unsure about the use of a given cleaner on a surface, please test it first on a small, inconspicuous area before proceeding with a broader cleaning program.
- These guidelines apply only to products manufactured by Steelcase. For guidance on cleaning other products, refer to the manufacturer of those products’ manufacturers.
- For custom materials (COM), contact the material manufacturer for cleaning guidelines.
- For guidelines specific to Designtex fabrics, refer to instructions on their website.
- Steelcase cannot make a determination of the effectiveness of a given disinfectant product in fighting pathogens, such as COVID-19. Please refer to your local public health authority’s guidance on how to stay safe from potential infection.